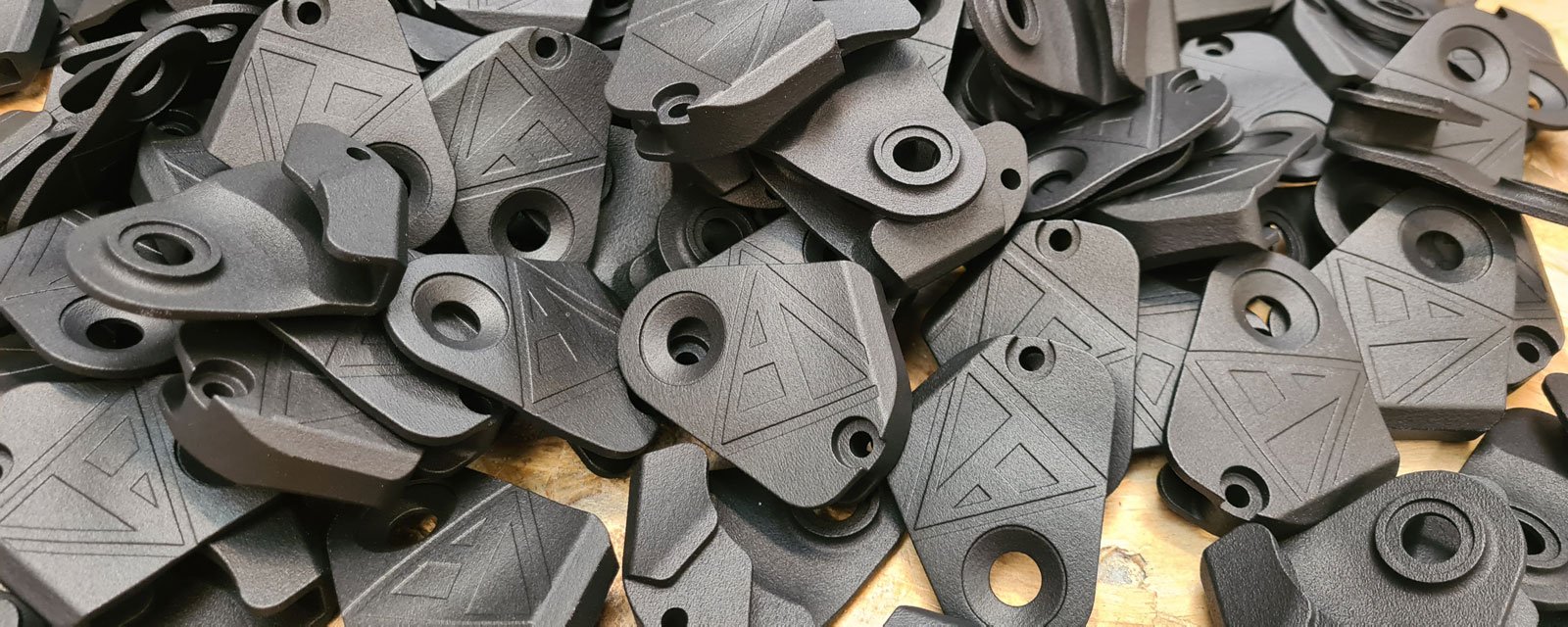
PLASTIC COMPONENT MANUFACTURING FOR PRODUCT STARTUPS.
We understand that dilemma; it’s one we had ourselves before we started using additive manufacturing.
No Tooling
Injection moulding tooling is a large investment to make on a new to market product. Quantities for small and complex components may be in the 10,000s before the injection moulding amortised part costs become less than MJF.
Design freedom
Component design for MJF production have far fewer design constraints than injection moulding, CNC or other processes:
No draft angle considerations
No consideration of undercuts required
No support structures
Parts can be printed captured inside an outer part
We can work with you or you industrial design agency to optimise your design to take advantage of this design freedom.
Get to market faster
Want to be first to market? The benefits of rapid prototyping using 3d printing are well known and using MJF for initial production means products can get to market faster and with less risk before bridging to injection moulding at higher volumes.
Make continual improvements
However much you test there are always improvements that don’t come to light until the product is in market. Using MJF a component’s design can be iterated or completely changed without expensive and slow tooling modification or scrapping 1000’s on mouldings. Lower risk.
Low Inventory
With no tooling parts can be ordered in small batches or JIT. No MOQs of 1000s, less money spent upfront on inventory.
Quickly respond to demand
Perhaps you need just a few extra components, instead of having to order 1000s we can produce as few as you need. Or you‘ve a received a large order, we can manufacture 1000s of components in days, no need to wait for a injection moulding press to be free.
Variants and customisation
A batch can contain as many component variations as you need, some clever boffins are also using data driven geometry to create 3D models that can then be printed.
Post process finishing
As well as the necessary powder removal we realised that finishing is vital in order to produce viable end use components. Our shot peening process give components a consistent texture common to many consumer goods. As well as a dyed black colour we can get products Cerakoted to give further colour and gloss level options.
Confidentiality and NDAs
We keep your projects confidential and will happily sign an NDA before discussing details with you.
You’ve got a great product idea, you want to get it on the market before anyone else but the capital investment in injection moulding tooling is high and the design has not yet been frozen.

Agrisound Case Study
Agrisound are an agritech startup that provides beekeepers with a range of hardware and software solutions for the remote management of hives. Established in 2020, AgriSound specialises in the use of low cost environmental and acoustic sensors to monitor bee dynamics.
They approached us wanting a quick turnaround solution to mounting solar panels on their devices. Using the design freedom offered by 3D printing we designed a one piece bracket that is 50% of the cost of the original 2 piece design. A prototype was delivered 1 week from brief with 60 production units delivered a week later.
We were able to custom design our AgriSound recording devices to work with Innocent's current design.
Research by our friends at University of Reading shows that yellow fluorescence can help to attract a broad variety of different pollinators to come into the detection zone.
Once in the zone, activity can be recorded by the microphone and data relayed back to the AgriSound web app.
Calum Pheby, Agrisound
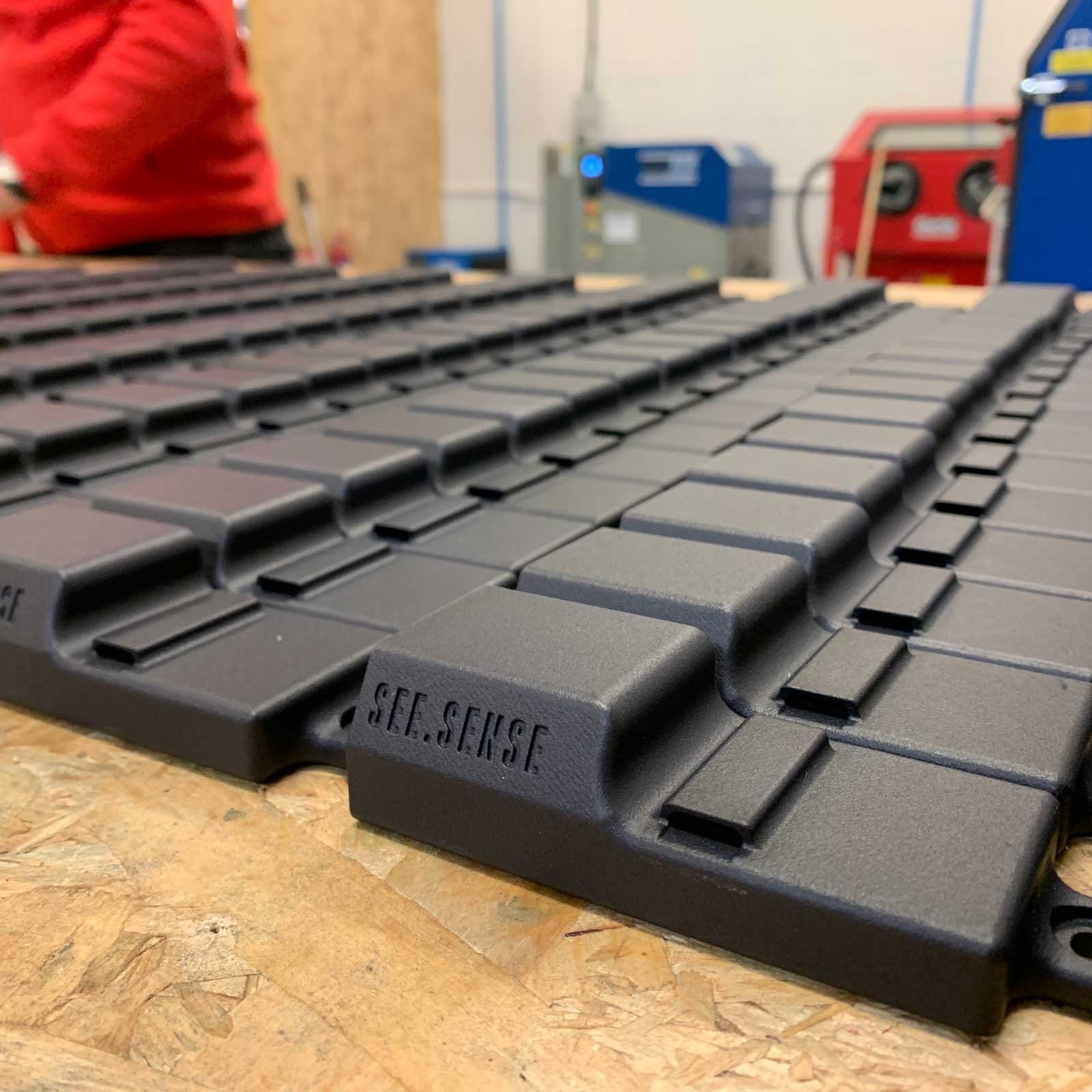
SeeSense Case Study
SeeSense are best know for their range of innovative smart bike lights that adapt to conditions, helping cyclists stay safe. They also produce tracking devices for rental eScooters and Ebikes for we manufacture the electronics enclosures.
The on-demand nature of additive manufacture means that each time a new city is signed up to the hire scheme a batch can be manufactured to suit the scheme size.
Our SUMMIT (Sensor Unlocked Micro-Mobility Insight Technology) tracker seamlessly integrates into bikes or e-scooters. Combining near-real-time GPS tracking, accurate positioning and low battery drain, with the ability to gather granular sensor data, we offer state of the art in micro-mobility monitoring and data insights.

76 Projects Case Study
76 Projects is our sister company. Their innovative bike components aimed at performance orientated cyclist have received awards and many top rated reviews as well as having been chosen by Pro Tour cycling teams and world champions. Over 50% of sales are exported including to Taiwan, the global powerhouse of the bike industry.
“When we founded 76 Projects we vowed never to release ‘me too’ products that only different in branding to what already existed. Only products that are genuinely innovative or a significant improvement can make the grade.
It soon became obvious that most components design s in the market were compromised. Either because of injection moulding’s or CNC’s inherent design constraints or because in order to justify the tooling costs and MOQs the design of the products were negatively compromised in order to appeal to a wider customer base.
Multi Jet Fusion allows us to release products with several variants to meet different riders needs with no tooling it’s viable to have products that sell in hundreds per years as opposed to the ten of thousands required my major brands that use injection mouldings.
Talking to others in the bike industry and beyond made us realise how additive manufacturing can benefit so many SMEs, hence we launched 76 Additive ”
Rob Johnson, Co-founder, 76 Projects