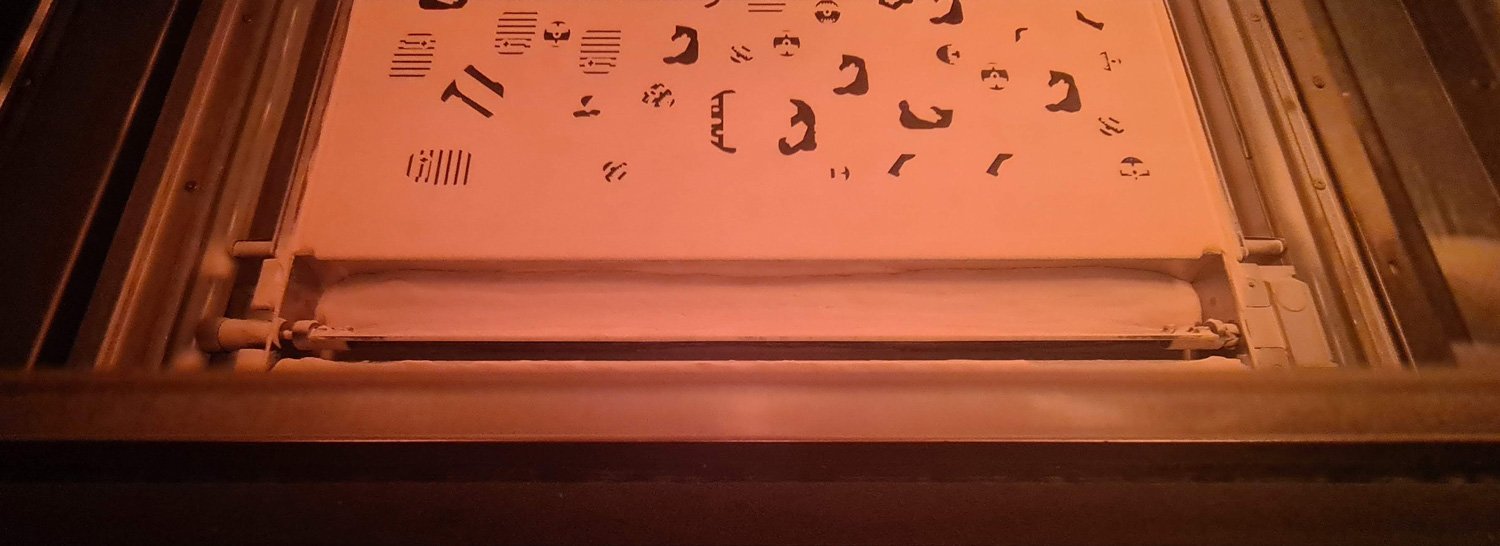
MJF 3D PRINT TECHNOLOGY.
HP Multi Jet Fusion (MJF) is a powder-bed fusion 3D printing technology that allows for the production of accurate, functional prototypes and end use parts. Unrivalled speed, accuracy and repeatability make it ideal for batch manufacturing.
The entire process is managed at our dedicated Print Lab, based in Cambridgeshire.
The Benefits of Additive Manufacturing
SPEED
3D printing can generate rapid prototype iterations in order to get to market faster, with the ability to deliver hundreds - or sometimes thousands - of components within a matter of days.
REPEATABLE QUALITY
Our MJF Parts are consistent, reliable and of comparable quality to injection mouldings.
LOW RISK, NO INVESTMENT
With no tooling investments or Minimum Order Quantities, you can test the market with small initial runs and make iterative design improvements, keeping your total cost of ownership low compared to other manufacturing methods.
AGILE SUPPLY CHAIN
On-demand production helps you produce new variants, reduce transport costs and keep your inventory under control.
DESIGN FREEDOM
Free from the constraints of injection moulding or CNC, additive manufacturing can produce components that would otherwise be physically or financially impossible. You can even customise components within batch runs.
SUSTAINABLE
Choose from a range of environmentally friendly materials including PA11, which creates super-strong components with minimal environmental impact.
How Does it Work?
Watch the video opposite to learn more about how Multi Jet Fusion 3D printing works.
If you’d like to find out about our order process and hear from some of our previous customers, visit our Working with Us page.
Print the impossible
The MJF process does not require support structures, thus enabling the design of complex geometries which would be prohibitively expensive or not even possible to produce with traditional manufacturing processes.
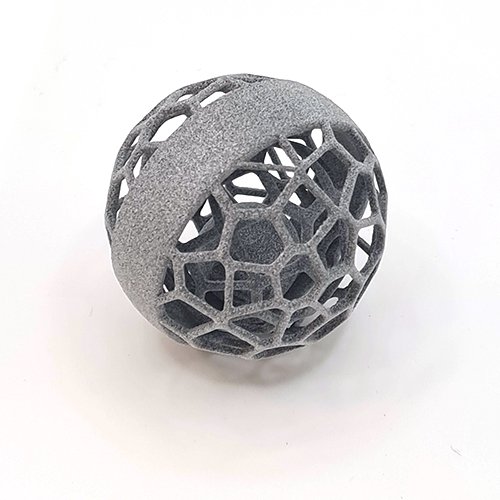
Multiple body objects
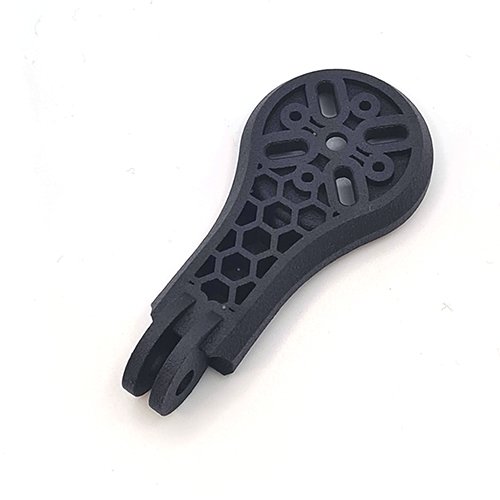
Optimise material use
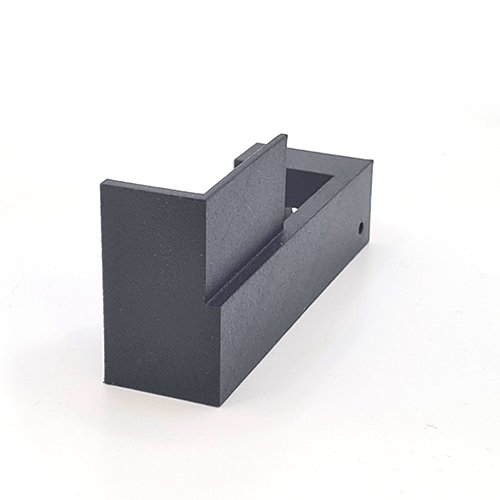
Draft angles not required
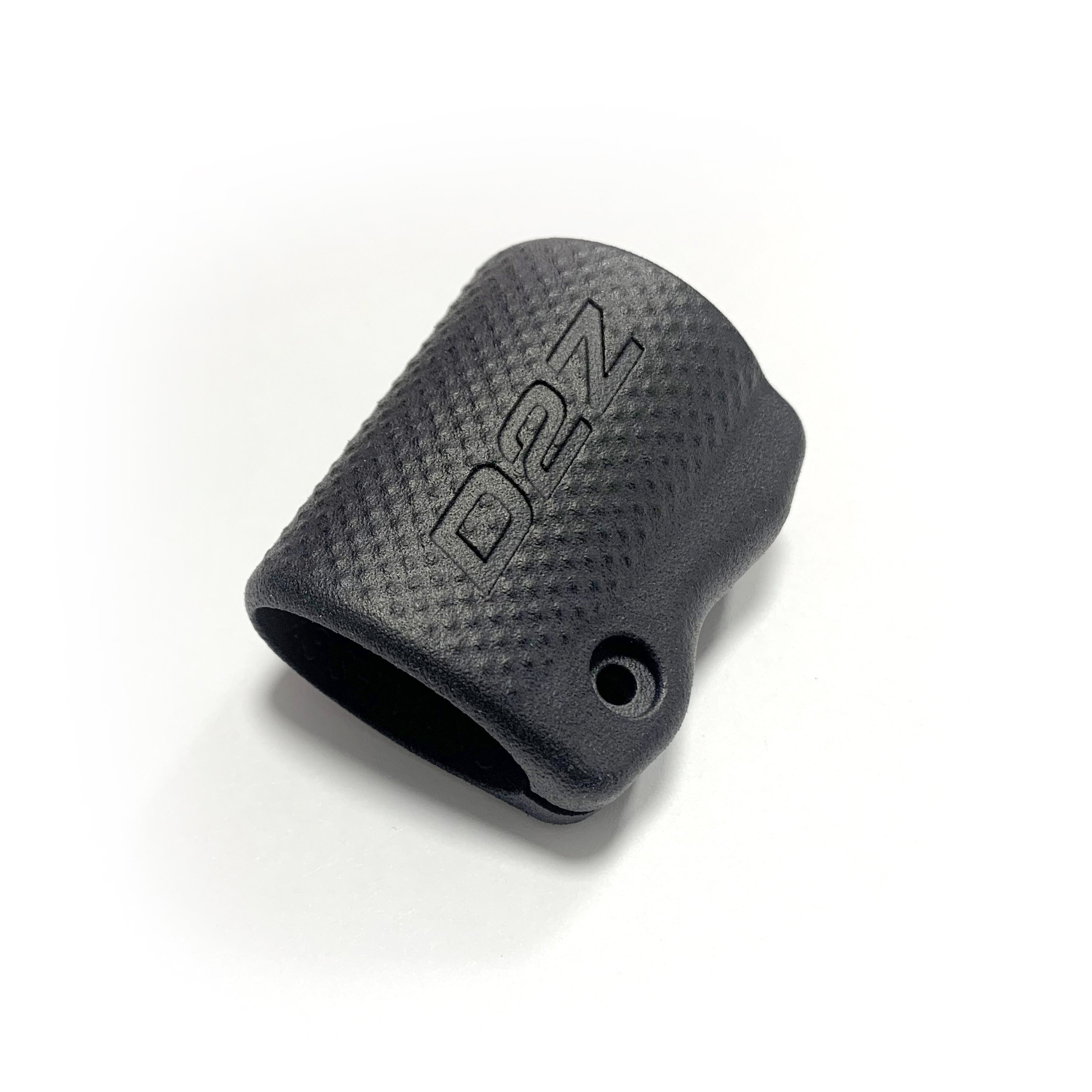
Logos and texture
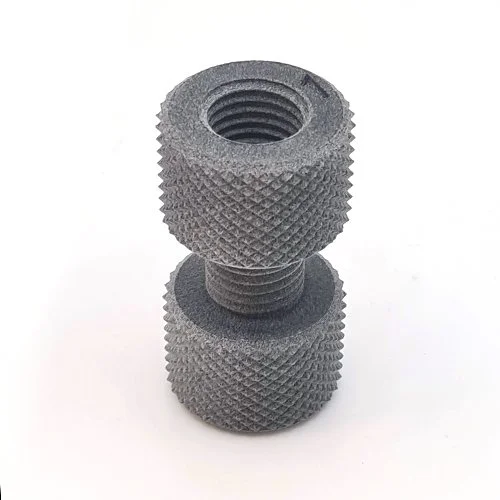
Working threads
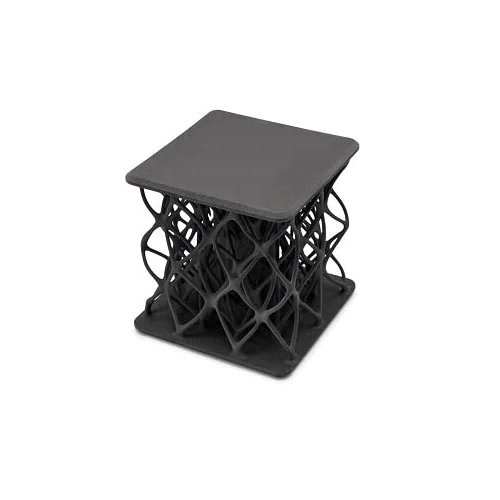
Lattice Structures
FREE SAMPLE FIDGET SWATCH
Your specially-made fidget swatch is a fun stress-relief toy that will let you experience the quality and accuracy of MJF additive manufacturing for yourself.
Best of all, it’s free, and with no obligation. Order yours now and see how it compares for your next project before you invest in tooling.